Revolutionizing Wind Turbine Inspections: A Vision-Based Approach to Damage Detection Using Deep Learning
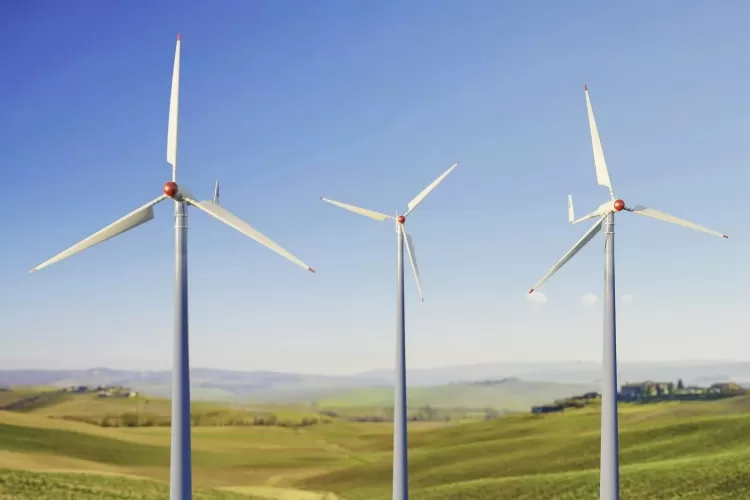
As the demand for renewable energy continues to grow, the infrastructure that supports it—particularly wind turbines—faces increasing challenges. Wind turbines, vital to sustainable energy production, are exposed to a wide range of stresses that can compromise their performance and lifespan. Traditional methods for detecting damage, such as manual inspections or non-destructive testing (NDT), are labor-intensive, costly, and susceptible to human error. But what if we could replace these outdated methods with faster, more reliable, and automated systems?
This is where the power of deep learning and computer vision comes in. In a recent study, researchers explored the application of cutting-edge deep learning techniques to detect and classify damage in wind turbine structures using vision-based approaches. The study used advanced algorithms like YOLOv7 and Faster R-CNN to automate damage detection and real-time monitoring, potentially transforming how we maintain these critical structures.
Understanding the Core Concepts
To understand this study, let's first break down some key concepts:
-
Structural Health Monitoring (SHM): This involves assessing the health of structures like wind turbines to ensure they are safe, functional, and reliable. Traditional methods often involve visual inspections and manual testing, but these are becoming outdated due to their time-consuming and error-prone nature.
-
Deep Learning and Computer Vision: These fields involve using algorithms to analyze and interpret visual data. Convolutional Neural Networks (CNNs) are particularly useful for image analysis, including tasks like detecting cracks, corrosion, and other forms of structural damage.
-
YOLOv7 and Faster R-CNN: Both of these algorithms are state-of-the-art models for real-time object detection. YOLOv7, in particular, is known for its speed and efficiency, making it ideal for real-time monitoring. Faster R-CNN, on the other hand, is a more complex model that excels in precision, although it can be slower in comparison.
The Challenge Addressed by the Research
The study addresses several significant challenges in traditional methods of damage detection:
-
High Costs and Safety Risks: Manual inspections and NDT methods are costly and often require specialized equipment and trained personnel. Moreover, these methods pose safety risks, especially when inspectors have to operate in hazardous conditions such as on tall turbines or offshore locations.
-
Time-Intensive Processes: Traditional inspection methods are slow, which can delay the detection of critical damage and lead to costly downtime for the turbines.
-
Human Error: Visual assessments are prone to subjectivity and human error, potentially leading to missed or misclassified damage.
The authors of the study set out to tackle these limitations by harnessing the power of deep learning algorithms to automate and improve the accuracy of damage detection.
A New Approach: The Authors' Contribution
The research team employed three advanced algorithms—YOLOv7, its lightweight variant, and Faster R-CNN—to detect and classify wind turbine damage. They trained the models using a dataset of wind turbine surface images, including various damage categories like cracks, corrosion, and pollution, while also augmenting the dataset to improve model training.
-
YOLOv7: This model was the standout performer in the study, achieving an impressive accuracy of 82.4% mAP@50. It also demonstrated exceptional speed, making it well-suited for real-time inspections.
-
Faster R-CNN: While slower than YOLOv7, this algorithm achieved higher precision in detecting smaller or low-contrast damage. However, its slower execution speed made it less ideal for real-time applications.
By optimizing the hyperparameters—such as learning rate and batch size—the researchers were able to further enhance the models' accuracy and computational efficiency. These results are particularly promising for industries that require rapid, cost-effective, and scalable damage detection solutions.
Implications for the Field
The implications of this research are far-reaching:
-
Practical Applications: Vision-based deep learning techniques like YOLOv7 can significantly reduce the costs and risks associated with traditional inspection methods. Real-time monitoring systems powered by these algorithms could be deployed on wind turbines, especially in remote or offshore locations where manual inspections are challenging.
-
Future Research: The study also highlighted some challenges, such as the limitations of the dataset and variability in environmental conditions. Future work could focus on developing segmentation methods and expanding the dataset to address these issues. Additionally, researchers could explore how to apply these techniques to other infrastructure, such as bridges or pipelines.
Conclusion: A Step Forward in Structural Health Monitoring
This research marks an important step forward in the field of structural health monitoring. By integrating deep learning and computer vision, the study demonstrates how we can automate damage detection, improving accuracy, speed, and safety while reducing costs. YOLOv7, in particular, shows great potential in real-time monitoring applications, offering a scalable solution for maintaining critical infrastructure like wind turbines.
As we continue to push the boundaries of technology, the potential for vision-based damage detection systems to revolutionize industries like renewable energy is immense. These systems not only promise to improve the efficiency and reliability of infrastructure maintenance but also contribute to a more sustainable and safe future.
What’s Your Take?
How do you think AI-powered damage detection systems could shape the future of infrastructure maintenance? Will they become the standard in industries beyond renewable energy? Let us know your thoughts in the comments!
What's Your Reaction?
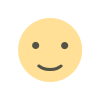
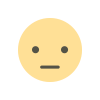
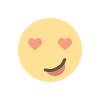
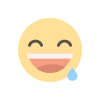
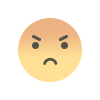
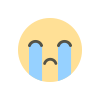
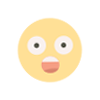