Crafting Safety: The Process of Making Tempered Glass and Pouches...!!!
Both tempered glass and stand-up pouches undergo meticulous manufacturing processes to ensure their strength, durability, and functionality. These processes highlight the importance of quality control and material selection in producing reliable and safe products.
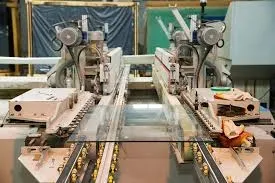
Tempered Glass Manufacturing Process
Tempered glass, also known as toughened glass, is a type of safety glass that undergoes controlled thermal or chemical treatments to enhance its strength compared to ordinary glass.
1. Selection of Raw Materials
The process begins with the selection of high-quality raw materials, mainly silica sand, soda ash, limestone, and feldspar. These materials are carefully measured and mixed to ensure the final product's strength and clarity.
2. Melting
The raw materials are melted in a furnace at temperatures reaching up to 1500°C (2732°F). This intense heat transforms the mixture into a viscous liquid. The molten glass is then refined to remove any remaining gas bubbles or impurities that could compromise its structural integrity.
3. Cutting
Once the glass is in its molten state, it is cut into the desired size and shape using specialized cutting equipment. This step ensures that the glass meets the specific requirements for its intended use.
4. Inspection and Cleaning
The cut glass is inspected for any flaws such as cracks, bubbles, or inclusions. Any imperfections are removed to prevent breakage during the tempering process. The glass is then thoroughly cleaned to remove dust, dirt, and debris.
5. Heating
The cleaned glass is heated in a tempering furnace at temperatures over 600°C (1112°F). This heating process ensures that the glass reaches a uniform temperature throughout.
6. Quenching
After heating, the glass undergoes a rapid cooling process known as quenching. High-pressure blasts of cold air are directed at the glass from varying angles for about 3 to 10 seconds. This rapid cooling creates a state of compression on the surface and tension in the interior, making the glass several times stronger than regular glass.
7. Testing and Inspection
The tempered glass is tested for strength, durability, and quality. This ensures that it meets the required standards for its intended application.
Pouches Manufacturing Process
Stand-up pouches, also known as doypacks, are a popular form of flexible packaging used for various products. Here’s an overview of the manufacturing process:
1. Determining the Purpose
The first step is to determine the specific use of the pouch, whether it is for food, pharmaceuticals, or other products. This helps in selecting the appropriate materials and design features.
2. Designing
A conceptual design is created using compatible software to draw a virtual representation of the pouch. This design process includes decisions on features such as zippers, spouts, and tear notches.
3. Material Selection
The right materials are selected based on the intended use of the pouch. Common materials include composite plastics like PET/PE and kraft paper for a more sustainable option.
4. Printing
The outermost layer of the pouch is printed with branding messages and other information using alcohol-based inks. This layer often bears the company name and other marketing details.
5. Lamination
The different layers of the pouch are laminated together to create a single, multi-layered structure. This process ensures that the pouch is waterproof and airtight.
6. Cutting and Sealing
The laminated material is cut into the desired shapes and sizes. The individual parts of the pouch are then sealed together using heat.
7. Quality Testing
The finished pouches undergo quality tests to ensure they meet the required standards for durability, functionality, and aesthetics.
Both tempered glass and stand-up pouches undergo meticulous manufacturing processes to ensure their strength, durability, and functionality. These processes highlight the importance of quality control and material selection in producing reliable and safe products.
What's Your Reaction?
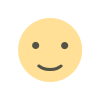
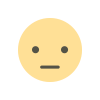
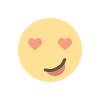
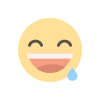
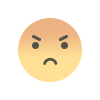
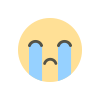
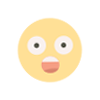